Plastik hissələrin dizaynı necədir
Qısa Təsvir:
Üçün plastik hissələrin dizaynıhissələrin məhsulda oynadığı rola və plastik üçün qəlibləmə prosesinin qaydasına əsasən hissələrin formasını, ölçüsünü və dəqiqliyini təyin etməkdir. Son nəticə kalıbın və plastik hissənin istehsalı üçün təsvirlərdir.
Məhsul istehsalı dizayndan başlayır. Plastik hissələrin dizaynı birbaşa məhsulun daxili quruluşunun, maya dəyərinin və funksiyasının reallaşmasını müəyyənləşdirir və eyni zamanda kalıp istehsalının növbəti mərhələsini, maya və dövrü, həmçinin enjeksiyon kalıplama və işlənmədən sonrakı prosesi və dəyəri müəyyənləşdirir.
Plastik hissələr müasir cəmiyyətdə müxtəlif məhsullarda, obyektlərdə və insanların həyatında geniş istifadə olunur. Plastik hissələr fərqli forma və funksiyalar tələb edir. Plastik materiallardan istifadə edirlər və xüsusiyyətləri müxtəlifdir. Eyni zamanda sənayedə plastik hissələr hazırlamağın bir çox yolu var. Buna görə plastik hissələrin dizaynı sadə bir iş deyil.
Fərqli hissə dizaynı və material fərqli işlənmə ilə istehsal olunur. Plastik tökmə emalı əsasən aşağıdakıları əhatə edir:
1. enjeksiyon kalıplama
2. üfürmə
3. sıxılma qəliblənməsi
4. ratsional qəlibləmə
5. termoformasiya
6. ekstruziya
7. fabrikasiya
8. köpüklənmə
Bunları kütləvi şəkildə istehsal etməyin bir çox yolu var. Enjeksiyon kalıplama məşhur istehsal üsuludur, çünki enjeksiyon kalıplı% 50 ~% 60 plastik hissələr byb enjeksiyonla istehsal olunur, yüksək sürətli istehsal qabiliyyətidir.
Dizayn etdiyimiz bəzi plastik hissələr üçün kassanı göstərin:
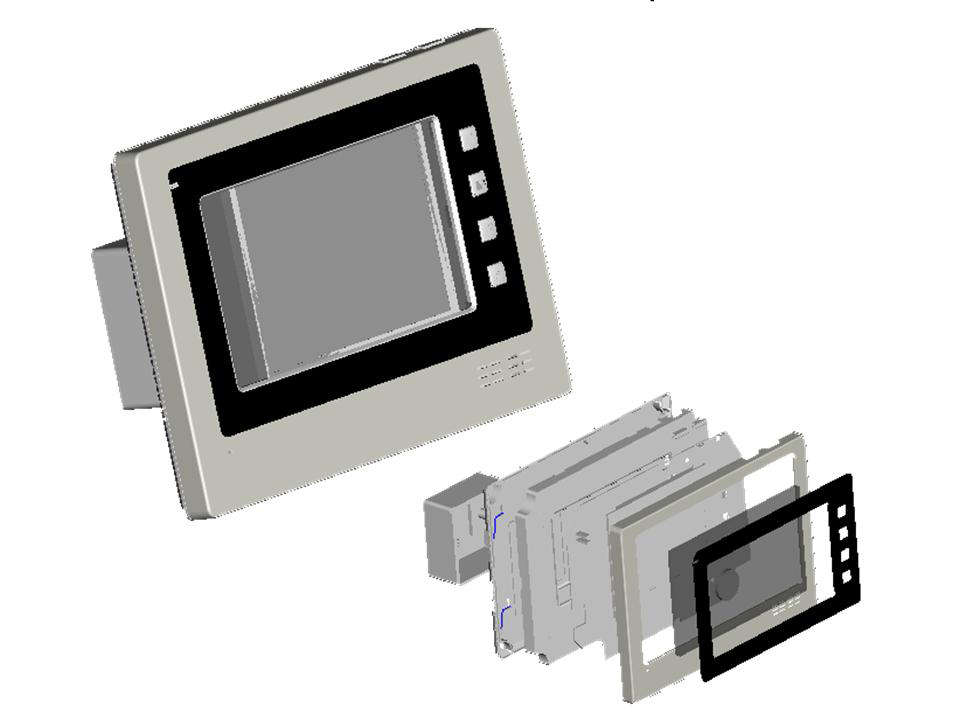
Görmə telefonunun plastik qapağı
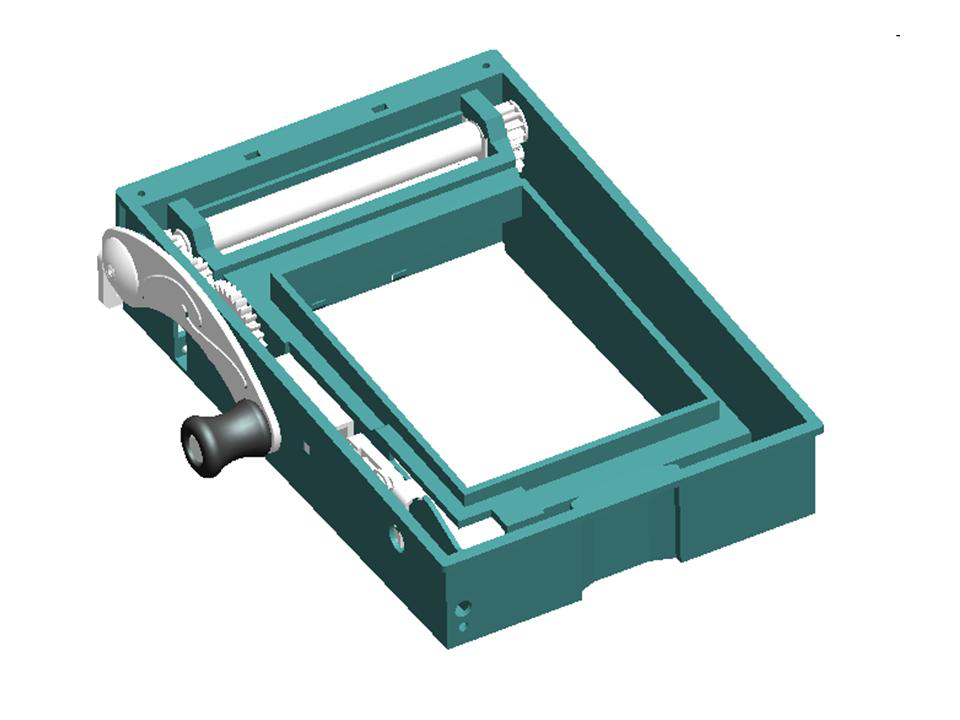
Mexanizmin plastik hissələri
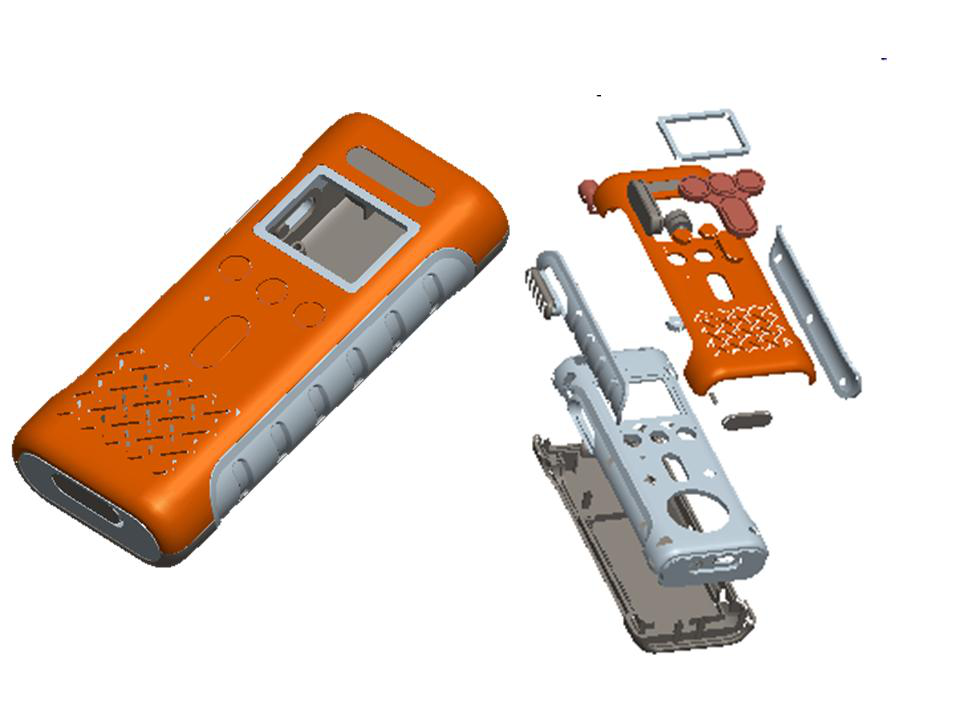
Plastik elektron qutular
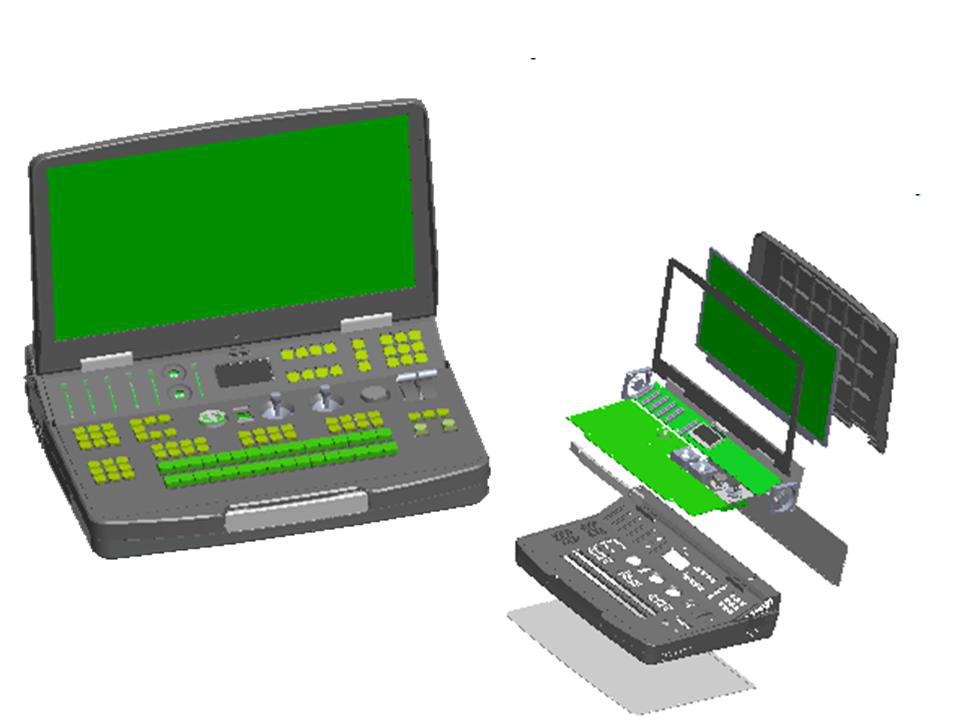
Alət üçün plastik korpus
Aşağıda plastik hissələrin üç cəhətdən necə dizayn ediləcəyi barədə ətraflı məlumat paylaşırıq
* Bilməli olduğunuz plastik hissələrin dizaynı üçün 10 tövsiyə
1. Məhsulun görünüş dizaynını və ölçüsünü təyin edin.
Bu, bütün dizayn prosesində ilk addımdır. Bazar araşdırmalarına və müştərilərin tələblərinə görə məhsulların görünüşünü və funksiyasını müəyyənləşdirin və məhsul hazırlamaq vəzifələrini formalaşdırın.
İnkişaf tapşırığına əsasən, inkişaf qrupu məhsulun texniki və texnoloji texniki-iqtisadi təhlilini aparır və məhsulun 3D görünüş modelini hazırlayır. Sonra funksiyanın reallaşdırılmasına və məhsul yığılmasına görə mümkün hissələr planlaşdırılır.
2. Fərdi hissələri məhsul rəsmlərindən ayırın, plastik hissələr üçün plastik qatran növü seçin
Bu addım, hissələri əvvəlki addımda əldə edilmiş 3D modeldən ayırmaq və fərdi olaraq dizayn etməkdir. Parçaların funksional tələblərinə uyğun olaraq uyğun plastik xammal və ya hardware materialları seçin. Məsələn, ABS ümumiyyətlə
qabıq, ABS / BC və ya PC-nin müəyyən mexaniki xüsusiyyətlərə, abajur, PMMA və ya PC post lampa kimi şəffaf hissələrə, dişli və ya POM və ya Naylon hissələrə sahib olması tələb olunur.
Parçaların materialını seçdikdən sonra detal dizaynına başlamaq olar.
3. Qaralama açılarını təyin edin
Qaralama açıları, plastikin qəlibdən çıxarılmasına imkan verir. Döşəmə açıları olmadan, hissə, çıxarılma zamanı sürtünmə səbəbindən əhəmiyyətli bir müqavimət göstərə bilər. Qaralama açıları hissənin içində və xaricində olmalıdır. Hissə nə qədər dərindirsə, qaralama açısı o qədər böyükdür. Sadə bir qayda, düym başına 1 dərəcə bir açı bucağına sahib olmaqdır. Çatdırılma bucağının olmaması hissənin kənarları boyunca qırıntılara və / və ya böyük ejektor pininin işarələrinə səbəb ola bilər (daha sonra bu barədə).
Xarici səthin açı bucaqları: Hissə nə qədər dərindirsə, çəkmə bucağı o qədər böyük olur. Sadə bir qayda, düym başına 1 dərəcə bir açı bucağına sahib olmaqdır. Çatdırılma bucağının olmaması hissənin kənarları boyunca qırıntılara və / və ya böyük ejektor pininin işarələrinə səbəb ola bilər (daha sonra bu barədə).
Ümumiyyətlə, yaxşı bir görünüş səthinə sahib olmaq üçün hissələrin səthində toxuma hazırlanır. Dokulu divar kobud, sürtünmə böyükdür və onu boşluqdan çıxarmaq asan deyil, buna görə daha böyük bir rəsm açısı tələb olunur. Daha kobud toxuma, daha böyük tərtib bucağına ehtiyac duyur.
4. Divar qalınlığını / bərabər qalınlığını təyin edin
Aşağıdakı səbəblərə görə enjeksiyonda qatı forma qəliblənməsi istənilmir:
1) .Soğutma müddəti divar qalınlığı kvadratı ilə mütənasibdir. Qatı üçün uzun soyutma müddəti, kütləvi istehsal iqtisadiyyatını məğlub edəcəkdir. (zəif istilik keçiricisi)
2) .Qalın hissə daha incə hissədən daha çox büzülür, bununla da diferensial büzülmə tətbiq olunur və nəticədə ştamp və ya lavabonun işarəsi və s. (Plastiklərin büzülmə xüsusiyyətləri və pvT xüsusiyyətləri)
Buna görə plastik hissə dizaynı üçün əsas qaydaya sahibik; divar qalınlığı mümkün qədər vahid və ya hissədən sabit olmalıdır. Bu divar qalınlığına nominal divar qalınlığı deyilir.
Hissədə möhkəm bir hissə varsa, nüvəni təqdim edərək içi boş olmalıdır. Bu, nüvənin ətrafında bərabər divar qalınlığını təmin etməlidir.
3) .Duvar qalınlığına qərar vermək üçün nələr nəzərə alınmalıdır?
İş üçün kifayət qədər qalın və sərt olmalıdır. Divar qalınlığı 0,5 ilə 5 mm arasında ola bilər.
Daha sürətli soyumaq üçün kifayət qədər incə olmalı, daha aşağı hissə ağırlığı və daha yüksək məhsuldarlıq ilə nəticələnməlidir.
Divar qalınlığındakı hər hansı bir dəyişiklik mümkün qədər minimum səviyyədə olmalıdır.
Müxtəlif divar qalınlığı olan plastik bir hissədə fərqli soyutma dərəcələri və fərqli büzülmə yaşanacaq. Bu vəziyyətdə yaxın dözümlülüyə nail olmaq çox çətin və dəfələrlə qeyri-mümkün olur. Divar qalınlığının dəyişməsinin vacib olduğu yerlərdə, ikisi arasında keçid tədricən olmalıdır.
5. Hissələr arasında əlaqə dizaynı
Ümumiyyətlə iki qabığı bir-birinə bağlamalıyıq. Daxili komponentləri (PCB montajı və ya mexanizm) yerləşdirmək üçün aralarında qapalı bir otaq yaratmaq.
Adi əlaqə növləri:
1). Çəngəllər:
Snap kancalar bağlantısı ümumiyyətlə kiçik və orta ölçülü məhsullarda istifadə olunur. Xarakterik cəhəti budur ki, qarmaqlar ümumiyyətlə hissələrin kənarına qoyulur və məhsul ölçüsü daha kiçik edilə bilər. Yığıldıqda, tornavida, ultrasəs qaynaq kalıbı və digərləri kimi alətlərdən istifadə edilmədən birbaşa bağlanır. Dezavantaj, qarmaqların qəlibin daha mürəkkəb olmasına səbəb olmasıdır. Sürgü mexanizmi və qaldırıcı mexanizm, qarmaqlar bağlantısını həyata keçirmək və kalıp maliyetini artırmaq üçün lazımdır.
2). Vida birləşmələri:
Vida birləşmələri möhkəm və etibarlıdır. Xüsusilə, vida + qoz fiksasiyası çox etibarlı və davamlıdır, çatlar olmadan bir çox sökülməyə imkan verir. Vida bağlantısı böyük kilidləmə gücünə və çoxsaylı sökülməyə malik məhsullar üçün uygundur. Dezavantaj vida sütununun daha çox yer tutmasıdır.
3). Montaj patronları:
Bossların birləşdirilməsi, patronlar və deliklər arasındakı sıx koordinasiya ilə iki hissəni düzəltməkdir. Bu əlaqə yolu məhsulları sökməyə imkan verəcək qədər güclü deyil. Dezavantaj, sökmə vaxtı artdıqca kilidləmə gücünün azalmasıdır.
4). Ultrasonik qaynaq:
Ultrasonik qaynaq, iki hissəni ultrasəs kalıbına qoyaraq və təmas səthini ultrasəs qaynaq maşınının təsiriylə birləşdirməkdir. Məhsul ölçüsü daha kiçik ola bilər, enjeksiyon kalıbı nisbətən sadədir və əlaqə möhkəmdir. Dezavantaj ultrasəs kalıbının və ultrasəs qaynaq maşınının istifadəsidir, məhsul ölçüsü çox böyük ola bilməz. Sökdükdən sonra ultrasəs hissələri yenidən istifadə edilə bilməz.
6. Qısaltmalar
Alt qəliblər, kalıbın hər iki yarısının çıxarılmasına mane olan maddələrdir. Çıxışlar dizaynın istənilən yerində görünə bilər. Bunlar hissədə bir qaralama açısının olmamasından daha pis olmasa da, qəbuledilməzdir. Bununla birlikdə, bəzi altlıqlar zəruridir və / və ya qaçılmazdır. Bu hallarda lazımlıdır
alt qəliblər qəlibdəki sürüşmə / hərəkət hissələri ilə istehsal olunur.
Unutmayın ki, qəlib istehsal edərkən alt qatlar yaratmaq daha baha başa gəlir və minimuma endirilməlidir.
7. Dəstək qabırğa / köşklər
Plastik hissədəki qabırğalar hissənin sərtliyini (yük və hissə sapması arasındakı əlaqə) yaxşılaşdırır və möhkəmliyi artırır. Qabırğa istiqamətində ərimə axınını sürətləndirdikləri üçün qəlib qabiliyyətini də artırır.
Qabırğalar hissənin xarici görünüşlü səthlərinə maksimum gərginlik və əyilmə istiqamətində yerləşdirilir. Kalıbın doldurulması, büzülməsi və atılması qabırğa yerləşdirmə qərarlarını da təsir etməlidir.
Şaquli divarla birləşməyən qabırğa birdən bitməməlidir. Nominal divara tədricən keçid stres konsentrasiyası riskini azaltmalıdır.
Qabırğa - ölçülər
Qabırğaların aşağıdakı ölçüləri olmalıdır.
Qabırğa qalınlığı, lavabonun işarəsinin qarşısını almaq üçün nominal divar qalınlığının 0,5 ilə 0,6 misli arasında olmalıdır.
Qabırğa hündürlüyü nominal divar qalınlığının 2,5 ilə 3 qat arasında olmalıdır.
Qabırğanın atılmasını asanlaşdırmaq üçün 0,5 ilə 1,5 dərəcə çəkmə bucağı olmalıdır.
Qabırğa bazası nominal divar qalınlığının 0,25 ilə 0,4 qat radiusuna malik olmalıdır.
İki qabırğa arasındakı məsafə nominal divar qalınlığından 2 ilə 3 qat (və ya daha çox) olmalıdır.
8. Radiasiya Edilmiş Kenarlar
İki səth birləşəndə bir künc meydana gətirir. Küncdə divar qalınlığı nominal divar qalınlığının 1,4 qatına qədər artır. Bu, diferensial büzülmə və qəliblənmiş stres və daha uzun soyutma vaxtı ilə nəticələnir. Buna görə kəskin künclərdə xidmətdə uğursuzluq riski artır.
Bu problemi həll etmək üçün köşeler radiusla düzəldilməlidir. Radius xaricdə olduğu kimi daxili də təmin edilməlidir. Çatmağı artırdığı üçün heç vaxt daxili iti küncünüzə sahib olmayın. Radius elə olmalıdır ki, daimi divar qalınlığı qaydasını təsdiq etsinlər. Künclərdə divar qalınlığının 0,6 - 0,75 qat radiusunun olması üstünlük təşkil edir. Çatmağı artırdığı üçün heç vaxt daxili iti küncünüzə sahib olmayın.
9. Vida patron dizaynı
Hər zaman iki yarıyı birlikdə düzəltmək və ya PCBA və ya digər komponentləri plastik hissələrə bağlamaq üçün vintlərdən istifadə edirik. Beləliklə, vida patronları sabitlənmiş hissələrə vidalanmaq üçün bir quruluşdur.
Vida patronu silindrik formadadır. Patron ana hissə ilə ya da yan tərəflə əlaqələndirilə bilər. Yan tərəfdən bağlanma, qalın plastik hissəyə səbəb ola bilər, bu arzuolunmaz, çünki lavabonun işarəsinə səbəb ola bilər və soyutma müddətini artırır. Bu problem, eskizdə göstərildiyi kimi patronu qabırğadan yan divara bağlayaraq həll edilə bilər. Boss, qabırğa qabırğaları təmin edilərək sərtləşdirilə bilər.
Vida, başqa bir hissəni bağlamaq üçün patronda istifadə olunur. Vida tipli vida və protektorlu kəsmə tipli vintlər var. İplik əmələ gətirən vintlər termoplastiklərdə, sap kəsici vintlər isə elastik olmayan termoset plastik hissələrdə istifadə olunur.
İplik əmələ gətirən vintlər soyuq axınla patronun daxili divarında dişi saplar əmələ gətirir - plastik kəsilmək əvəzinə lokal deformasiyaya məruz qalır.
Vida rıçağı vida yerləşdirmə qüvvələrinə və vida üzərinə qoyulan yükə davamlı olaraq xidmətdə olmalıdır.
Çuxurun vidaya nisbətən ölçüsü, iplərin soyulmasına və vida çəkilməsinə müqavimət üçün vacibdir.
Boss xarici diametri iplik əmələ gəlməsi səbəbindən halqa gərginliklərinə davam gətirəcək qədər böyük olmalıdır.
Çuxur qısa bir uzunluq üçün giriş boşluğunda bir az daha böyük bir diametrə sahibdir. Bu, sürücülüyə başlamazdan əvvəl vida yerini tapmağa kömək edir. Üstəlik patronun açıq ucundakı stressləri azaldır.
Polimer istehsalçıları materialları üçün patronun ölçüsünü təyin etmək üçün təlimatlar verirlər. Vida istehsalçıları vida üçün uyğun delik ölçüsü üçün təlimatlar da verirlər.
Bossdakı vida dəliyi ətrafında möhkəm qaynaq birləşmələrini təmin etmək üçün qayğı göstərilməlidir.
Təcavüzkar mühitdə uğursuz ola biləcəyi üçün patronda yaranmış stresin qarşısını almaq üçün diqqətli olun.
Bossda olan çuxur iplik dərinliyindən daha dərin olmalıdır.
10. Səthi bəzək
Bəzən gözəl bir görünüş əldə etmək üçün tez-tez plastik qabın səthində xüsusi müalicə edirik.
Məsələn: toxuma, yüksək parlaq, sprey boya, lazerlə oyma, isti basma, elektrokaplama və s. Məhsulun dizaynında əvvəlcədən nəzərə alınmaq lazımdır, sonrakı işlənmənin əldə olunmaması və ya məhsulun yığılmasına təsir edən ölçü dəyişikliklərinin qarşısını almaq lazımdır.